ПРОК – производство ПВХ профиля
ПРОК – это полностью автономное, обособленное производство по выпуску ПВХ профиля, с замкнутым производственным циклом. Обрезки и отходы производства возвращаются на первую ступень и после измельчения повторно используются для приготовления смеси. Площадь занимаемая производственными помещениями 4000м2.
Как исходное сырье ПВХ получают в виде мелкого белого порошка. Чистый ПВХ не является конструкционным материалом. Для того чтобы его переработать в изделие с определенными эксплуатационными качествами, к порошку ПВХ добавляется целая рецептура аддитивов: стабилизаторы, смазки, наполнители, красители, модификаторы.
На сегодняшний день предприятие имеет мощную производственную базу на всех участках: от стадии подготовки сырья (автоматизированное приготовление смеси подачи её непосредственно до экструдера) до упаковки и реализации готового изделия. Смешивание составляющих происходит в миксере. Создание рецептуры композиции требует проведения исследовательских работ, лабораторных и промышленных испытаний – это работа для специалистов высокой квалификации.
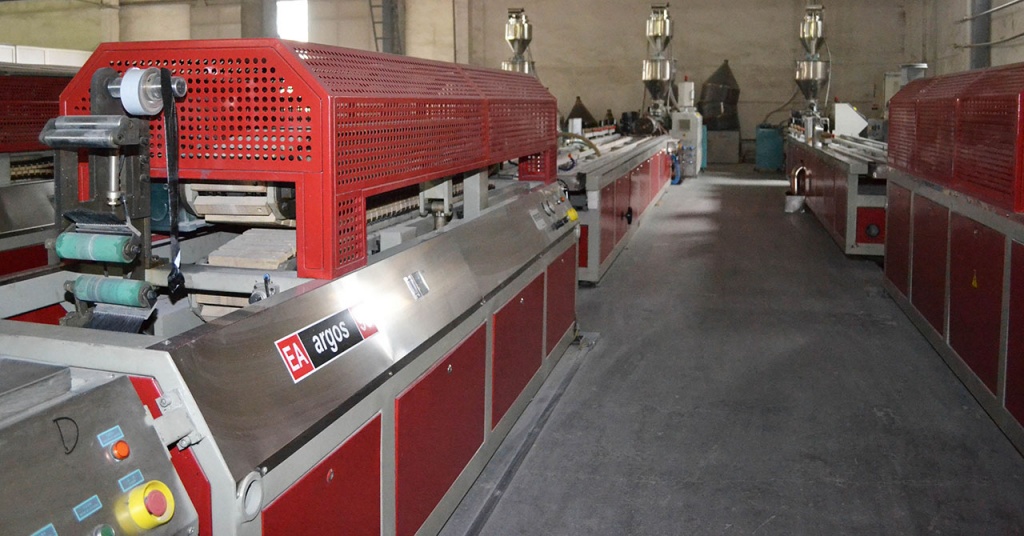
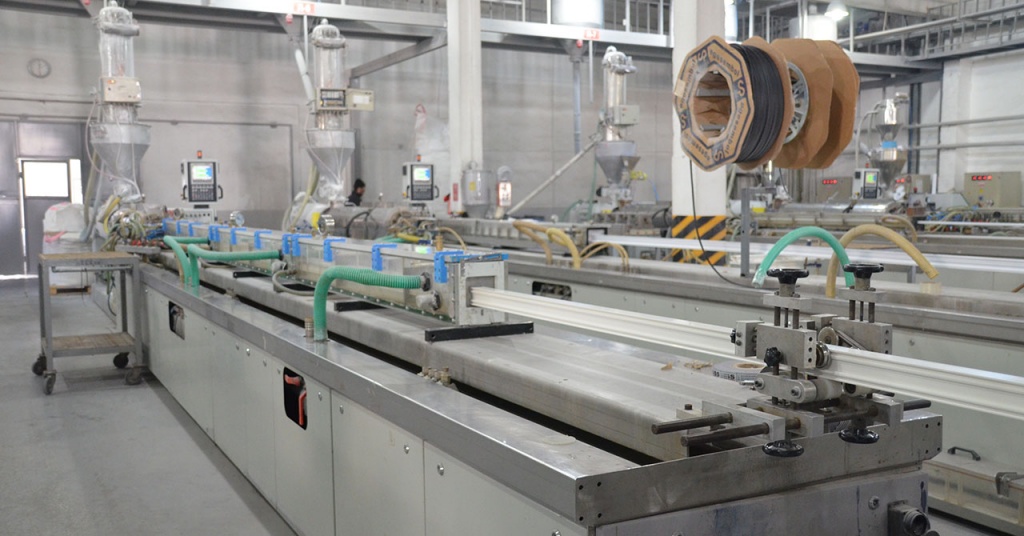
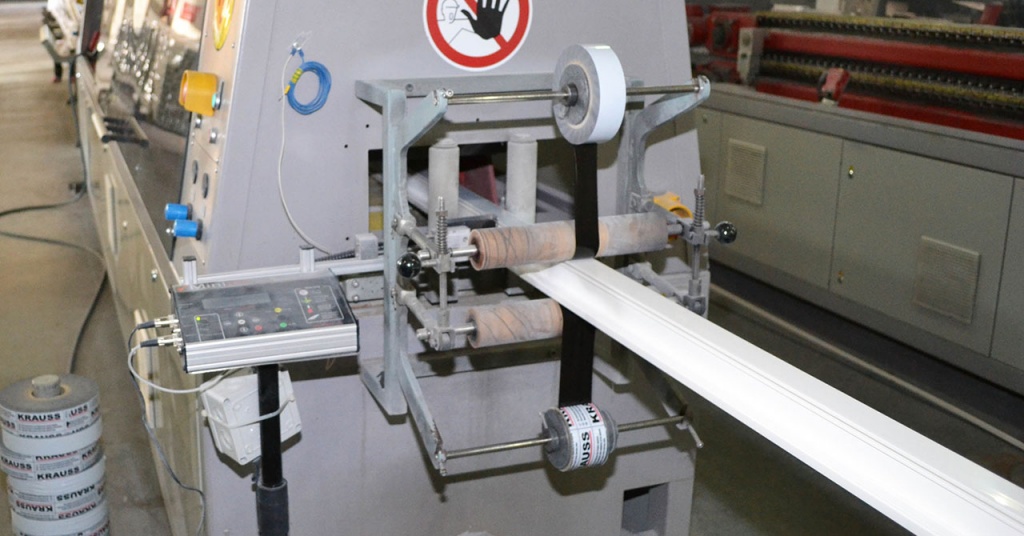
Экструзия
Смешение всех компонентов рецептуры проводится в три этапа: смешение в горячем смесителе, смешение в холодном смесителе, выдержка смеси при температуре 15-30 градусов в течение 24 часов. Подготовленная таким образом смесь подается в экструдер.
Экструзия - это способ изготовления профильных изделий большой длины из пластмасс и резины. Процесс непрерывен и заключается в выдавливании расплава полимера через отверстие определенного сечения. Первый шнековый экструдер для переработки термопластов был создан в Германии в 1935г. Функция экструдера состоит в обеспечении плавления непрерывно подаваемой твердой полимерной смеси, образовании гомогенного вязкого расплава и нагнетания расплава под высоким давлением в профильную головку. Производственная линия включает экструдер, инструмент (фильеру, устройство сухой и влажной калибрации), маркирующий принтер, тянущее устройство, пилу для резки профиля, устройство для укладки и упаковки готовой продукции.
Подготовленная смесь ПВХ подается в материальный цилиндр экструдера, захватывается шнеком и продвигается по зонам, температура обогрева которых повышается от 150-170 градусов на входе до 190-210 градусов на фильере. В первой зоне происходит перемешивание и предварительный разогрев материала. В следующей зоне пластикации материал переходит в вязкотекучее состояние, уплотняется и поступает в зону дегазации для удаления газообразных включений, захваченного воздуха и влаги. В последней зоне выхода создается давление материала необходимое для прохождения расплава через фильеру.
"Сердцем" всей экструзионной линии по праву считается инструмент: фильера и калибраторы. Именно инструмент в решающей степени определяет качество профиля и требует максимальной тщательности в своем производстве. Фильера состоит из матрицы и дорна, которые формируют щелевой канал протекания расплава. Таких линий на предприятии 15. Их суммарная производительность может достигать 70т. в сутки готовой продукции. Большое количество линий позволяет обеспечить широкий ассортимент выпускаемой продукции как по конфигурации профиля так и по цветовой гамме.
Собственная аккредитованная лаборатория обеспечивает контроль качества на каждом этапе производства, в том числе проводится и входной контроль получаемого сырья. Продукция имеет все необходимые сертификаты и отвечает высоким стандартам Российского рынка.
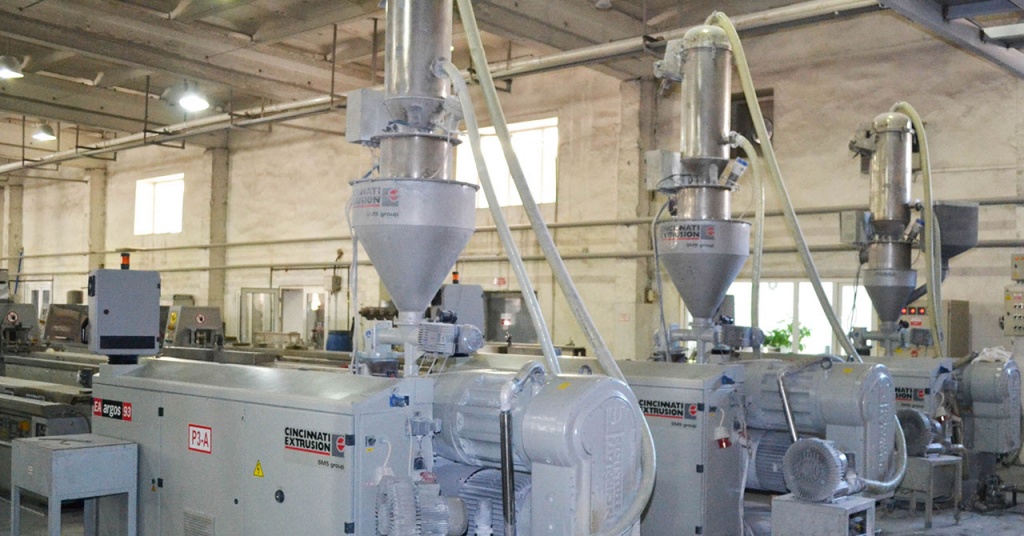